
Our DNV ISO 9001 CERTIFIED engineering phase
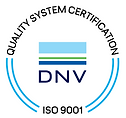
Our team is able to apply problem solving design techniques to modify an existing design for bespoke use, or provide blank page designs for challenges with no apparent solution.
With an eye for innovation, we can provide fresh perspective to your project, and ensure our work is practical and cost-effective to manufacture & install.
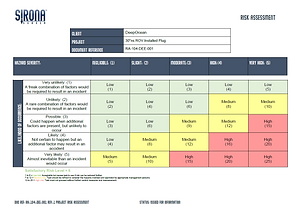
project risk assessment
We can effectively evaluate a projects likelihood of success by conducting a specific project risk assessment in conjunction with the technical specification. In doing so provides a seamless transition into concept design and development.
In short, we can utilise our experience of associated products to critique pre-determined designs and develop solutions for our clients' specification.
DESIGN INCEPTION
Utilising CAD software allows us to take an idea of 2D sketch to 3D-realistic visual representations. A concept lays the foundations for a product and therefore allows progression through subsequent phases for product realisation. Conceptualisation of ideas is one of the first steps in development, and utilising CAD allows swift manipulation and adjustment to fine-tune to a tangible product.
CAD files can be interrogated by our clients and suggestions made on the concept itself, resulting in a design per client expecations.

feed and feasibility study
Developing a bespoke product forms a fundamental aspect of devising a solution, however, there are instances where project loads and/or pressures present an area of concern.
In this instance, design calculations and FEA can be conducted to theoretically verify a system design, using recognised industry standards in conjunction with client specifications.
From conceptualised design, we can provide a full report to support product realisation. The study will assess the conceptualised design in line with client provided data, industry data and applicable standards. We have worked to or in accordance with the following;
With the correct standards identified, we can produce design calculations & finite element analysis (FEA), with more specialist techniques utilised where applicable.
The study can be complimented with a failure mode effect and criticality analysis (FMECA), third party design verification using the likes of Lloyds, DNV or BV or an alternative client preferred validation method. This would be controlled using our in-house project management expertise.
DESIGN calculations
A design report, inclusive of calculations, is compiled to provide mechanical analysis and theory for specific equipment. They are utilised to verify a products capacity to perform in operation when subjected to real-time conditions.
Calculations are typically conducted to recognised industry standards and include applicable levels of contingency, ensuring integrity in accordance with accidental load-cases or similar.
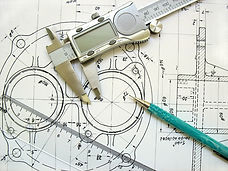
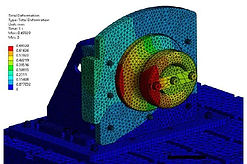
finite element analysis
Further to theoretical design validation by calculation, it is often worthwhile expanding upon to utilise simulation software to apply loads to a CAD model applying pessimistic project variables. This allows our engineering team to determine:
-
Design capabilities to withstand loadings
-
Identify areas of weakness or unnecessary strength
-
Areas in which could be adjusted to provide a more economical solution
DESIGN drafting
From design inception and concept refining, we can produce detail drawings allowing our clients' product to be manufactured.
This operation could come pre or post-FEED study.

project management [PM]
With over 500 successfully delivered projects within the oil, gas and renewable markets, our project management standards have been accepted and approved globally by energy companies such as BP & TAQA, and Tier 1 contractors such as Subsea 7, DF Subsea & Aker Solutions.
Our team have delivered on-time & on budget projects with a net value up to 5 million GBP, with multiple end client, client & sub-contractor interfaces managed successfully.
We can support with a small part of your project, or turnkey delivery. We can also provide offshore assistance for your installation campaign if applicable.
reporting and client liaison
The project management team have experience of governing multi-million pound projects, and understand the importance of managing each area of interest. We conduct progress reports on weekly, bi-weekly or monthly periods in order to effectively communicate status.
The progress report typically includes:
-
Project status
-
Budgeting and finance
-
Chronological timeline of events
-
Exhaustive multi-level schedule
-
Document Register and status
-
ITP and task status

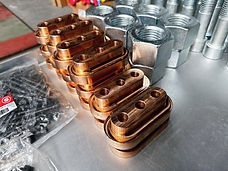
procurement and Receipt
We have expertise in this field, and utilise our company standard technique for management, which is a field-proven system.
Our system is repeated for all projects in accordance with our standard operating procedures, hence, we know each project will be executed with a high-level of quality.